Certainly someone in your organization inspects hand tools for wear and tear, cracking, or chipping. Grounds on electrical tools should be periodically checked as well as operational fitness.
But your employees and subcontractors bring tools on site too. Who checks those tools?
As a prime contractor, you are still responsible for overall workers’ compensation and general liability claims. Check their tools and personal protection equipment (PPE) too.
A fairly quick visual inspection will tell you if hard hats fit properly, whether or not workers have proper eye protection, are they dressed correctly for the work, and if they have appropriate footwear.
Take time to check any suspicious or missing PPE.
Check hand tools to assure quality: no spurs on hammers or chisels, handles securely attached, no cracks or breaks, nothing rusted shut or open? Saws sharp?
Inspect the cords on power tools. Are they grounded? No loose prongs? Are they appropriate for the application?
Most of these inspections can be done quickly and unobtrusively while the crew sets up their workspace. Ask if they have an assured grounding program, and if so, could you review the paperwork.
Offer to help correct any deficiencies. The idea is to work safely, not stop work completely.
Observe the safety attitude of these subcontractors. It’s one thing to have proper tools, PPE and work clothes. It requires discipline and good work habits to operate safely.
Tell and write your employees about your standards for proper tool maintenance. They should want to bring their own tools. You, however, are still responsible.
Certainly power tools must be properly grounded. Require these personal tools to be inspected and tagged as acceptable.
If OSHA visits the site and corporate tools undergo an inspection process, but personal tools do not, or if it’s significantly different, OSHA will rightfully have an issue with this protocol. You may still be in compliance, but sloppy habits point to greater potential problems.
Besides, don’t your employees deserve a safe workplace not invaded with dangerously maintained tools and ungrounded power equipment.
Observe the workforce, the entire workforce. Inspect tools to assure safety and proper maintenance. Require subcontractors and specialty labor to follow the same rules. Keep the workplace safe for all of them.
Before construction begins on any site, it’s a good idea to walk through your work. Excavation is a tricky operation because the operator must focus on surface down; however, some of the worst possible accidents can occur above the equipment.
First, have the utilities identified by the marking service operating in your area or state.
Overhead wires, cables, tree branches or structures can be struck by the boom if not properly managed. A walk-through helps select the proper equipment and point of attack.
Start by looking up. Any problems such as wires? Note them in the instructions for your operator.
Bring your eyes down to boom swing level. Parking areas, decks, office trailers, anything that can get hit by a boom needs to be noted.
Bring the utilities maps, existing and proposed, and double check locations. The markers and you can both make errors in location. Are all electrical lines and fiber optics located and in agreement with the utility plans? Any high pressure gas lines or pipelines?
Use white marking paint to layout your workspace. Can you excavate, load trucks and stockpile fill logically and safely? Ample ingress and egress for trucks? Minimum of trucks backing up?
Map the entire process out, make notes, and share them with your operator.
Okay, so why check from the top down?
The focus shifts to the trench, basement, utility or whatever operation you’re performing so naturally, that many people forget the big picture. The focus of the crew tends to stay downward once the operation begins. It is important to design the operation so the overhead exposures remain minimally invasive.
Any time in the process that the unexpected is encountered, for example the fiber optic line is twenty feet from where it shows on the existing plan, begin the inspection over again from that spot. Look up and begin.
Too many accidents occur when the equipment moves to accommodate a seemingly small adjustment, but nobody checks all three dimensions where the equipment operates. Get into the habit of top down.
Usually, installations begin from the lowest elevation and move to the highest. If you inspect from the top down, you will anticipate the shortest “ceiling” you’ll be working under. Mark that spot mentally and with white paint. That will be your most dangerous above ground impediment.
Remember: top down inspections for safe digging.
Electrocution safety – could there be too much vigilance? It happens so fast there’s no time to say oops or rethink.
One professional electrician, always thoughtful about his work, always safe, was splicing a wire to an outdoor light post. Of course he checked the line and there was no current. What he didn’t check was whether or not the light was on a timer. Be overly cautious.
The Occupational Safety and Health Administration (OSHA) requires Ground Fault Circuit Interruption (GFCI) protection on all jobsites unless a documented Assured Equipment Grounding Conductor Program (AEGCP) is in place.
For those unfamiliar with an AEGCP, the requirements are as follows:
1. The plan must be in writing and available on site, on demand.
2. The plan must schedule all inspections and procedures for taking equipment or tools out of service or bringing them back in.
3. Make one person responsible who knows how to spot a defect and has the authority to correct said defect.
4. Check all equipment, cords and receptacles prior to use every day. Take any defective equipment out of service.
5. OSHA requires a continuity test and a terminal connection test before the first use of any tool or equipment, after any repair and prior to returning to service, after suspected damage, and quarterly.
Certainly, your site will be protected by GFCI. This safety feature is marginally very low cost.
Doesn’t it make sense to implement a layer of redundancy, the AEGCP? First, it gives you a schedule to double check all your tools, cords and machines for safety. Second, it gives you a protocol for checking subcontractors and tools they bring to the site. Third, for the few minutes each day it takes to comply, you may save a colleague from electrocution.
Job site safety concerns avoiding situations which can cause injury. Grounding all electrical appliances is among the most important precautions you can take. The double check, the redundant system, the mindset to check to cut off power and check for those timers, create habits that can save lives.
Check your electric tools today to get started. Check the terminal connections and run the continuity test. Check your cords, any defects or missing prongs? Find the right person to establish and manage the AEGCP.
New Year’s Resolutions for Risk Managers
Whether your business has downsized or grown over the past few years, the waters seem a bit calmer now; and it’s a good time to overhaul your risk management program.
Resolve to address the trends in liability claims:
• Cyber liability is a rapidly growing source of claims. These claims tend to be costly in terms of reputation as well as expensive to mitigate. Spend some money avoiding these risks, particularly when you are on shared access on-site.
• Building Materials and supplies. The insurance industry is scared of finding the next asbestos claim. Do not use known toxic products in construction. Keep in mind environmental issues are an increasing source of claims. Indoor air quality is a near-future catch-all vector for asthma, CPOD, and other respiration conditions lawsuits. The formaldehyde sheet rock incident was quickly remediated; but use that as a lesson for mastic selection or supply sourcing.
• Keep your work space dry. Mold and mildew flourish at 15-18% moisture content. Before buttoning up closed spaces, take time with a moisture meter and record the results. This step is vitally important for new or replacement roofs. Dry these areas thoroughly until moisture content is below 15%.
• Employment practices. With a greater number of women entering and thriving in the construction industry, resolve to treat these valuable employees on equal terms with their male associates. And educate all employees about sexual harassment and bullying. Zero tolerance is your best written policy for this liability.
• The officers and directors of every public company are under attack from customers, employees, and regulators. Review your D&O coverage thoroughly.
Resolve to be more proactive than in the past. Check behind every delegated task. Personally walk sites, shops, offices, and site trailers to assure fire and life safety equipment is available and properly functioning. Verify OSHA logs and internal safety data is up-to-date and communicated properly.
Resolve to review your risk management program thoroughly and begin shopping your insurance coverage, including new insurance carriers early, at least 120 days before your preferred expiration date. Get in sync with your agent or new agent on this matter.
The turmoil of the construction industry has sent shockwaves through the insurance industry as well. Calmer times are ahead. Just be sure your one of the first ones settled.
No discipline breaks down faster on a job site than traffic control and storage space. The turf wars and project inertia follow. Democracy is a poor way to run traffic control. This regulation requires a czar, one person responsible for and with the authority to sheriff this aspect of sites.
Traffic management concerns efficiency and safety. Done well, the job is enhanced; done poorly, the job crashes to a halt.
Begin by surveying the surrounding roads which service the site. Are any noteworthy conditions present:
• Steep grades leading into the site: can they be avoided with an alternate route?
• Schools, factories, shopping malls, or any high traffic area or regular high pulse traffic events need to be time mapped and routes or delivery schedules altered, especially large, heavy or wide loads.
• Where are the frequently used pedestrian areas?
• Tolls or gates present?
• What is the speed limit on the site exit roadway? Do you need traffic control?
• Where do you have entrance options?
• Are there any overly sensitive stakeholder neighbors like environmental protection or historical areas?
• Is any street work scheduled not associated with your site?
These questions will guide a logical approach, entrance, exit and departure strategy.
Review the site plan. Will heavy or long trucks have the same access to storage as the smaller and lighter trucks? Are there critical pinch points that need to remain clear? Some general rules for devising a plan:
• Avoid exiting a site within one hundred feet of a traffic light. That’s a traffic jam begging to happen.
• Minimize backing up on site.
• Minimize truck traffic through worker foot paths.
• Site speed limit should be 5 mph max.
• Avoid storage and travel in sensitive or tree protection areas.
• Decide on site access for weather events – include forklift use on wet or icy ground conditions.
• Determine the rules for forklift use, what areas, flagmen, what storage access.
• Will truck tire washing be necessary? If so, is the water and traffic slow down manageable?
Most of site traffic management is logical as long as you mentally walk through the site construction plan. Start off site and work towards your storage areas and most difficult improvement access stations. Managing this issue in advance of the job start is essential. Supporting your traffic czar, critical.
Turbulence in the contracting business, probably at an all-time high. Businesses are shrinking or expanding constantly. As a risk manager, you must embrace reality and try to resolve the current state of affairs.
Start your renewal process today by comparing your policy estimated payrolls with the summary W-2 sheet produced by your accounting department (must be completed by February 1).
Review the 1099s and check these recipients against your files to assure certificate compliance and proper risk transfer techniques.
After reassessing your payroll exposures for the coming year, estimate your current premium. Talk to your agent about optional markets at that premium level, insurance companies have different appetites for different size risks. Find several appropriate insurers.
Many insurers now demand loss control inspections prior to commitment to offering any quote. Get your reports in order. Make sure loss control measures are in place and working. Order loss runs from your current carrier to have on hand.
Most important: leave enough lead time for the inspections to occur. At least ninety days, so new insurers can inspect your operations.
The insurance markets retool every few years and create new identities, new brands within the industry. Currently, insurance companies are deciding what size accounts they will seek, single lines like workers’ compensation or general liability, or supporting lines requirements: like workers’ compensation, general liability or automobile liability. Ask your agent what the current view is among their companies.
The key to having choices is starting early now. Don’t leave yourself at the mercy of the renewal carrier.
While your reassessing your policies, rethink your program as well. Your program consists of the risk management decisions that have subtle but important impacts on your insurance costs. For example: what is your best expiration date? In the construction industry, January first or April first are popular choices in a well-managed risk management program.
One secret within the insurance industry: rates tend to change on calendar quarters. If rates are increasing on April first, you can always renew on March thirty-first if you have enough lead time. But you need to know in advance and have friendly underwriters, and proactive agents.
Calendar quarters allow for government filings to be used as a basis for the insurance auditors, and audits go smoother. Corporate financial years can be good, especially if they fall on calendar quarters. Decide your best expiration date (and you want all liability lines to share that date)and begin 120 days in advance gathering quote information and loss data. Shop early.
Even professional football players need coaching about fundamentals. Observe the three point stances in the second quarter of any game.
Payroll determines base premiums for contractor’s key coverage: workers’ compensation and completed operations liability. Your company produces annual payroll recapitulations with summary reports for W-2s and 1099s at every year end.
Review estimated payroll given to your carriers for these policies. Does the comparison summary suggest a large additional premium or perhaps a return to your firm? If you discover a significant drop in payroll, which implies a significant decrease in premium, ask your agent to review the insurance carrier selection in light of this reality.
Some carriers prefer larger workers’ compensation or liability accounts and may choose to non-renew based on premium size. Check on this compatibility as part of your spring cleaning to-do list.
Calendar quarter expiration dates make sense since tax records get filed at these times. Self-audit becomes easier as do insurance company audits. If you do not now enjoy a calendar quarter expiration date, put that on your spring cleaning to-do list.
Review the 1099s. Do you have insurance certificates on file for these subcontractors? The insurance companies will charge premium for undocumented subcontractors. Check each one as an item on your list.
Check your contract status with each 1099 recipient to assure proper loss transfer language is in place.
Review OSHA logs, lunch-pail safety meeting, and similar in-house safety and injury reporting documentation for completeness and accuracy. Request loss runs from your insurance carrier. Does your information agree with their claims estimates?
Your experience rating is based on their estimates or “loss reserves”. Ask about any discrepancy in expectations.
Check your safety equipment such as fire extinguishers and first aid kits to assure they are up-to-date and functional. Do not delegate this task. Check them. This is life or death, not profit or loss.
So to recap your spring cleaning list:
• Review your W-2 and 1099 summaries and double check the associated documents.
• Review safety and loss documentation.
• Check life safety equipment personally.
Spring cleaning provides a pathway to a safe and efficient new year.
Most of us have heard of cold-related illnesses such as frostbite, hypothermia, chilblains, and trench foot. All are illnesses related to cold stress. But the cold is insidious and works its way deep into the body where it indirectly causes cold-related problems.
Workers with chronic diseases such as asthma or arthritis are more likely to suffer flare-ups in cold weather.
Cold stress also decreases the worker’s dexterity, coordination, mental skills, and causes an overall decline in performance that negatively affects worker safety. Workers are more prone to accidents.
Also, working in the cold increases the likelihood of employee sprains and strains. This turns up as a health issue such as a low back strain. However, all muscles and tendons have less resistance to harm when exposed to cold weather.
What is Cold Stress?
Cold stress is the way your body responds cold temperatures stemming from heat escaping from part of your body, such as hands, limbs, feet, and/or head. When the body has prolonged contact with cold, lengthy exposure is a physical and mental challenge to your body.
Humans lose heat four ways:
•Radiation
•Convection
•Conduction
•Evaporation
The best way to avoid cold weather stress leading to cold weather illness or injury involves changing work habits and wearing the right clothing.
Changing Work Habits
How long an employee works in cold weather depends on wind and air temperature. The colder the temperature and the stronger the wind, the shorter work periods are. The following table, adopted by the American Conference of Governmental Industrial Hygienists (ACGIH) as Threshold Limit Values (TLVs) for cold stress is an excellent guide for management in establishing the length of a work period.
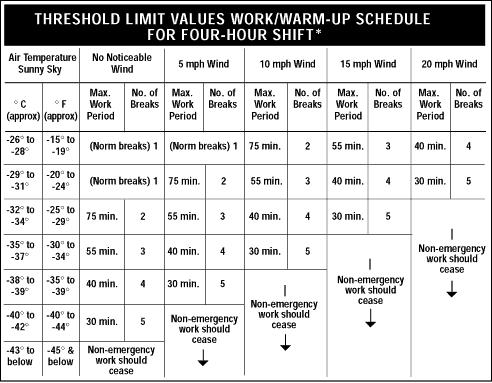
*Source: Adapted from Threshold Limit Values (TLV) and Biological Exposure Indices (BEI)
When workers are continuously exposed to below freezing temperatures shelters for warming such as heated tents, trailers or restrooms are in order for management to offer.
•Layer your clothing for better protection than one single heavy garment.•Wear thermal underwear made of polyester or polypropylene to wick away sweat.•The layers over the thermals should give you adequate insulation for the weather you are working in and be easily removed if you begin sweating too much. Your outer jacket should have a way to seal off the cuffs, waist, and neck. These seals should open easily if you become warm.•If there is rain or snow, make sure your outerwear is waterproof•Make sure to wear a watch cap or full ski mask – 50 percent of body heat is lost from your head.•Keep clothing clean since dirt infiltrates clothing fibers and ruins its ability to insulate.•Cover your hands with waterproof covering if the weather is wet. For very cold weather consider mittens.•Footwear made with rubber bottoms, leather uppers, and removable felt insoles are best for working in cold weather. Layer your socks using one pair of thin socks as the inner layer made of nylon, thin wool, or silk. Avoid cotton as it absorbs more water and does not wick away sweat. For the top layer wear a thicker sock. Bring several pairs of socks with you while working in the cold.•If you need face or eye protection make sure that the eye protection is separate from the nose and mouth protection. A single unit will cause the protection to fog us and blind you temporarily.
Construction is the industry with the most injuries and fatalities in the United States. To make the industry safer and cut the number of employee injuries and fatalities, the federal government, state governments and even local government passed laws mandating safety committees, their make-up, and even meeting content. Nevertheless, there are many reasons why construction companies should embrace safety committees.
How Safety Committees Benefit Construction Companies
Talk to a safety professional and you soon realize that the most effective committees are committees that involve members from every level of the company or a company facility or job site.
When company executives and laborers and everyone between them participate, safety committees help prevent unsafe work practices and environments. Committees also cut employee exposure work-related injuries and illnesses. These accomplishments spur other employees to get involved in the company’s workplace injury and illness programs.
An active safety committee shows employees that the company care about employee health and safety; itself a motivator that improves productivity.
Another bottom line enhancer is that a strong safety record cuts workman’s compensation claims and in turn, reduces workman’s comp premiums.
When safety records are impressive, construction job sites are safer and accidents to visitors and passersby go down. In turn, premiums for commercial general contractor policies may plateau or even go down.
Moreover, a safe workplace record impresses project owners and makes a construction company a more attractive candidate for selection.
Measuring Safety Committee Value
Many companies mistakenly undervalue the value of environmental health and safety programs (EHS). Companies usually do not measure EHS correctly if at all. But, by using standard tools in the toolbox of business managers and in a way that executives understand company financial statements. Results of EHS can integrate and display as part of the overall EHS business strategy. Some popular tools used by EHS professionals to measure the return on investment (ROI) of EHS include:
Six Sigma
EMS/ISO 1400
Baldwin Measurement
OSHA offers a tool called Safety Pays that helps figure out the ROI for a company’s safety program.
No matter what tool a company uses, construction companies that are committed to safety almost always sees a higher ROI for its efforts when compared to companies for which the safety committee is simply a means for compliance.